In the modern industrial landscape, where efficiency and safety are crucial, clamp lifters are essential yet often overlooked. These devices, operating from small workshops to large – scale factories, handle materials with precision, transforming industrial operations.
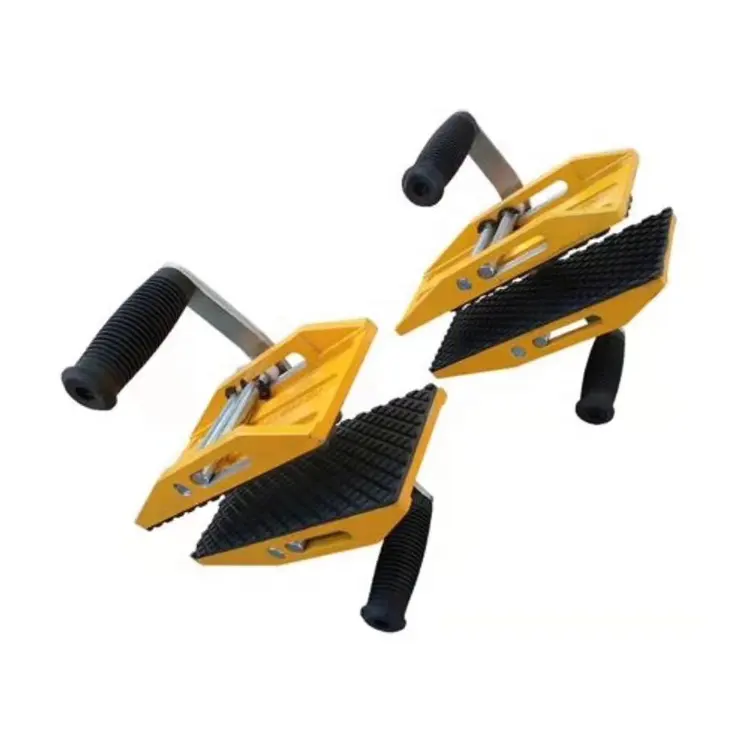
Scissor Clamp Lift
1. Unraveling the Intricate Design and Functionality
At the very essence of a clamp lifter lies a mechanical design that is a remarkable engineering achievement. It features a sturdy framework constructed from high – tensile alloys, capable of withstanding substantial forces. Attached to this framework are the jaws, which are the key components for gripping.
These jaws are precision – engineered, not simple parts. For example, when designed for handling cylindrical objects such as large – diameter pipes in the oil and gas industry, they are curved to match the pipe’s shape, ensuring a tight and secure hold.
The power sources for clamp lifters vary according to the industries they are used in. In heavy – duty shipbuilding, where massive steel plates need to be moved, hydraulic – powered clamp lifters are highly favored. They use a network of high – pressure hoses and cylinders. When hydraulic fluid is pressurized and flows through the system, it generates a force comparable to that of a small locomotive. This force is then transferred to the jaws, enabling them to open and close with enough strength to lift multi – ton steel sheets.
In the fast – paced electronics manufacturing industry, pneumatic clamp lifters are the preferred choice. They operate on compressed air, which is directed through a series of valves into a pneumatic cylinder. The advantage of this system is its speed. In just a few milliseconds, the piston in the cylinder can move, causing the jaws to quickly open or close, making it ideal for rapidly handling delicate circuit boards.
2. Applications Spanning Multiple Industries
In pharmaceutical manufacturing, where sterility and precision are essential, clamp lifters play a vital role. For instance, in the production of large – scale fermentation tanks used in manufacturing life – saving drugs, these stainless – steel tanks need to be moved and positioned with great care. Specialized clamp lifters with non – contaminating gripping surfaces are used. They can lift the tanks without introducing any impurities, ensuring the integrity of the drug – making process.
In the growing field of renewable energy, especially in wind turbine installation, clamp lifters are indispensable. Wind turbine blades, which can be over 100 meters long, are some of the largest and most delicate components to handle. Clamp lifters designed with extra – wide jaws and shock – absorbing mechanisms are used to lift these blades during installation. The shock – absorbing feature is crucial as it protects the blades from sudden jolts during the lifting process, which could potentially damage the blades’ aerodynamic properties.
3. Advantages that Set Clamp Lifters Apart
Safety is a fundamental aspect of clamp lifter design. Many modern models are equipped with advanced sensor – based safety systems. Some have load – cell sensors that continuously monitor the weight being lifted. If the load exceeds the rated capacity even slightly, an alarm is triggered, and the lifting mechanism stops immediately. There are also proximity sensors that detect any obstructions in the path of the jaws, preventing potential collisions.
Clamp lifters are not restricted to handling standard – shaped objects. In the art restoration industry, for example, where irregularly shaped and fragile artworks need to be moved, custom – designed clamp lifters are employed. These can be adjusted to fit the unique contours of sculptures or large – format paintings. By using soft, non – abrasive gripping materials, they can hold these precious artworks securely without causing any damage.
4. The Multifarious Types of Clamp Lifters
In the domain of small – scale industrial undertakings and for those with a do – it – yourself penchant, hand – actuated clamp lifters present a highly practical solution. These are typically crafted from high – strength aluminum alloys, a material choice that cleverly balances weight reduction and long – lasting sturdiness. Their operational mechanism is centered around a straightforward lever system.
This simple setup empowers the operator to manually manage the opening and closing actions of the jaws. Despite their uncomplicated design, they possess the capacity to hoist loads of up to several hundred kilograms. This makes them a fitting choice for tasks such as hoisting small engine components within a local auto repair shop.
Conversely, in large – scale manufacturing facilities, automated clamp lifters are bringing about a revolutionary change in the production workflow. These advanced lifters are seamlessly integrated with robotic manipulators and are governed by intricate computer – based algorithms. Through precise programming, they are capable of executing a sequence of lifting and positioning operations with remarkable exactitude.
For instance, within an automotive assembly facility, an automated clamp lifter can deftly pick up a car door from the production station. It then rotates the door to the precise orientation required and attaches it to the car body with an accuracy measured in millimeters.
5. Maintenance and Safety Protocols: The Bedrock of Sustainable Reliability
Sustained and regular maintenance is the linchpin for ensuring the long – term, trouble – free operation of clamp lifters. This maintenance routine encompasses a thorough inspection of the mechanical elements, with a particular focus on the hinges that link the jaws to the main frame. These hinges demand regular lubrication using a specialized anti – corrosion lubricant.
This not only safeguards against rust formation but also ensures that the movement of the jaws remains smooth and unhindered. In the case of hydraulic and pneumatic systems, vigilant monitoring and adjustment of fluid levels and air pressure are essential. These adjustments must be carried out in strict accordance with the manufacturer’s specifications.
Furthermore, operators of clamp lifters are required to undergo in – depth safety training. This training equips them with a comprehensive understanding of load – rating charts, enabling them to accurately assess the appropriate load – handling capacity of the equipment. They are also schooled in proper emergency – shutdown procedures.
During the training, operators are taught to identify the early warning signs of potential equipment malfunctions, such as abnormal vibrations or unusual noises during operation. Additionally, they are trained to utilize safety equipment like hard hats and safety gloves while operating the clamp lifter.
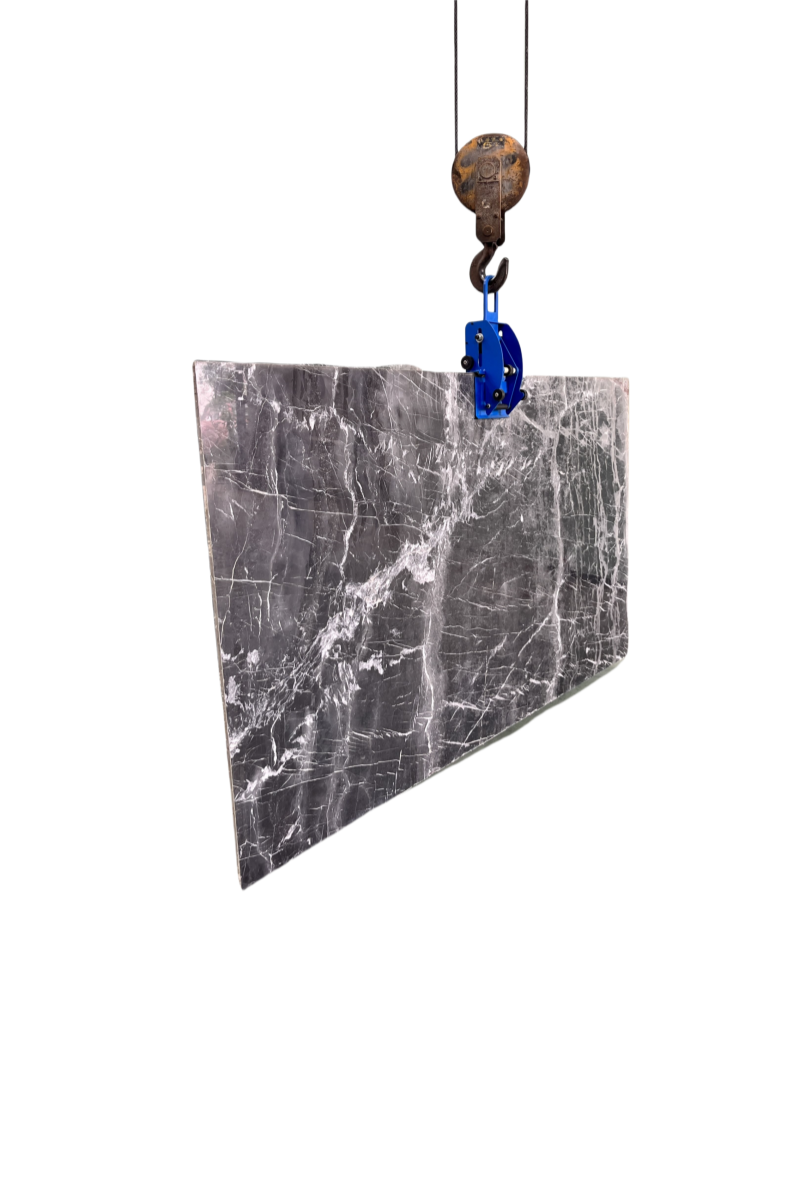
slab clamp lifter application
Clamp lifters are far from being ordinary lifting apparatuses. They are the unheralded champions that enable a vast array of industries to function with both efficiency and safety. Their distinctive design, extensive range of applications, numerous advantages, and the critical importance of proper maintenance and safety all contribute to their pivotal role in the contemporary industrial ecosystem.
As technological innovation continues to progress, it is reasonable to anticipate that clamp lifters will evolve into even more advanced and sophisticated tools, further augmenting their significance across diverse industrial sectors.